From: blaisb
Date: Tue, 12 May 2020 02:55:50 +0000 (-0400)
Subject: - Changed the default values for the parameters for the 2D case. The default case...
X-Git-Tag: v9.2.0-rc2~3^2~4
X-Git-Url: https://gitweb.dealii.org/cgi-bin/gitweb.cgi?a=commitdiff_plain;h=38c8765bfa518f9ffaba1074af627e38020c4652;p=dealii.git
- Changed the default values for the parameters for the 2D case. The default case should run easily and produce better results
- Finalized resulted for the 2D case
- Minor modifications to introduction
---
diff --git a/examples/step-70/doc/intro.dox b/examples/step-70/doc/intro.dox
index 588219a43a..31e51e68e7 100644
--- a/examples/step-70/doc/intro.dox
+++ b/examples/step-70/doc/intro.dox
@@ -13,12 +13,11 @@
Massively parallel non-matching grid simulations of fluid structure interaction problems
In this tutorial we consider a mixing problem in the laminar flow regime.
-They occur in a wide range of applications ranging from chemical engineering to power
+Such problems occur in a wide range of applications ranging from chemical engineering to power
generation (e.g. turbomachinery). Mixing problems are particularly hard to solve numerically,
because they often involve a container (with fixed boundaries, and possibly
complex geometries such as baffles), represented by the domain $\Omega$,
and one (or more) immersed and rotating impellers (represented by the domain $\Omega^{\text{imp}}$).
-
The domain in which we would like to solve the flow equations is the (time
depedendent) difference between the two domains, namely:
$\Omega\setminus\Omega^{\text{imp}}$.
diff --git a/examples/step-70/doc/results.dox b/examples/step-70/doc/results.dox
index a4d4b41c2d..43a12c9c76 100644
--- a/examples/step-70/doc/results.dox
+++ b/examples/step-70/doc/results.dox
@@ -51,10 +51,10 @@ subsection Stokes Immersed Problem
set Homogeneous Dirichlet boundary ids = 0
# Initial mesh refinement used for the fluid domain Omega
- set Initial fluid refinement = 3
+ set Initial fluid refinement = 5
# Initial mesh refinement used for the solid domain Gamma
- set Initial solid refinement = 3
+ set Initial solid refinement = 5
set Nitsche penalty term = 10
set Number of time steps = 11
set Output frequency = 1
@@ -90,7 +90,7 @@ subsection Stokes Immersed Problem
# If the function you are describing represents a vector-valued function
# with multiple components, then separate the expressions for individual
# components by a semicolon.
- set Function expression = t < .500001 ? 5 : -5 # default: 0
+ set Function expression = t < .500001 ? 6.283185 : -6.283185 # default: 0
# The names of the variables as they will be used in the function,
# separated by commas. By default, the names of variables at which the
@@ -116,10 +116,11 @@ subsection Stokes Immersed Problem
end
subsection Refinement and remeshing
- set Maximum number of cells = 1000
+ set Maximum number of cells = 20000
set Refinement coarsening fraction = 0.3
set Refinement fraction = 0.3
- set Refinement maximal level = 5
+ set Refinement maximal level = 8
+ set Refinement minimal level = 5
set Refinement step frequency = 5
set Refinement strategy = fixed_fraction
end
@@ -177,7 +178,7 @@ subsection Stokes Immersed Problem
set Fluid bounding boxes extraction level = 1
set Homogeneous Dirichlet boundary ids = 0
set Initial fluid refinement = 5
- set Initial solid refinement = 3
+ set Initial solid refinement = 5
set Nitsche penalty term = 100
set Number of time steps = 501
set Output frequency = 1
@@ -186,7 +187,7 @@ subsection Stokes Immersed Problem
set Viscosity = 1
subsection Angular velocity
set Function constants =
- set Function expression = t < .500001 ? 5 : -5
+ set Function expression = t < .500001 ? 6.283185 : -6.283185 # default: 0
set Variable names = x,y,t
end
subsection Grid generation
@@ -198,10 +199,11 @@ subsection Stokes Immersed Problem
set Solid grid generator arguments = -.5, -.1: .5, .1: false
end
subsection Refinement and remeshing
- set Maximum number of cells = 1000
+ set Maximum number of cells = 20000
set Refinement coarsening fraction = 0.3
set Refinement fraction = 0.3
- set Refinement maximal level = 7
+ set Refinement maximal level = 8
+ set Refinement minimal level = 5
set Refinement step frequency = 5
set Refinement strategy = fixed_fraction
end
@@ -238,69 +240,117 @@ parameters to their default value.
The default problem generates a co-dimension zero impeller, consisting of a
rotating rectangular grid, where the rotation is for half a second in one
direction, and half a second in the opposite direction, with constant angular
-velocity equal to five.
+velocity equal to $\approx 2\Pi rad/s$. Consequently, the impeller does half a rotation
+and returns to it's original position. The following animation displays
+the velocity magnitude, the motion of the solid impeller and of the
+tracer particles.
-
-The output of the program will look like the following:
+On one core, the output of the program will look like the following:
@code
-bash$ mpirun -np 8 ./step-70 test.prm
+bash$ mpirun -np 1 ./step-70 test.prm
Running StokesImmersedProblem<2> using Trilinos.
Cycle 0:
Time : 0, time step: 0.002
Number of degrees of freedom: 9539 (8450+1089 -- 0+0)
-Tracer particles: 753
-Solid particles: 576
- Solved in 142 iterations.
- Number of degrees of freedom: 3790 (3354+436 -- 576+753)
+Tracer particles: 337
+Solid particles: 9216
+ Solved in 158 iterations.
+ Number of degrees of freedom: 9845 (8722+1123 -- 9216+337)
Cycle 1:
Time : 0.002, time step: 0.002
- Solved in 133 iterations.
+ Solved in 142 iterations.
Cycle 2:
Time : 0.004, time step: 0.002
- Solved in 148 iterations.
+ Solved in 121 iterations.
Cycle 3:
-
+Time : 0.006, time step: 0.002
+ Solved in 121 iterations.
...
-
Cycle 499:
Time : 0.998, time step: 0.002
- Solved in 167 iterations.
+ Solved in 199 iterations.
Cycle 500:
Time : 1, time step: 0.002
- Solved in 156 iterations.
-
+ Solved in 196 iterations.
+---------------------------------------------+------------+------------+
-| Total wallclock time elapsed since start | 46.9s | |
+| Total wallclock time elapsed since start | 302s | |
| | | |
| Section | no. calls | wall time | % of total |
+---------------------------------+-----------+------------+------------+
-| Assemble Nitsche terms | 501 | 0.73s | 1.6% |
-| Assemble Stokes terms | 501 | 1.34s | 2.8% |
-| Initial setup | 1 | 0.000827s | 0% |
-| Output fluid | 502 | 2.92s | 6.2% |
-| Output solid particles | 502 | 1.58s | 3.4% |
-| Output tracer particles | 502 | 2.04s | 4.4% |
-| Refine | 100 | 1.2s | 2.6% |
-| Set solid particle position | 500 | 0.213s | 0.45% |
-| Set tracer particle motion | 501 | 1.13s | 2.4% |
-| Setup dofs | 101 | 0.82s | 1.7% |
-| Solve | 501 | 35.4s | 76% |
+| Assemble Nitsche terms | 501 | 43.3s | 14% |
+| Assemble Stokes terms | 501 | 21.5s | 7.1% |
+| Initial setup | 1 | 0.000792s | 0% |
+| Output fluid | 502 | 31.8s | 11% |
+| Output solid particles | 502 | 32.2s | 11% |
+| Output tracer particles | 502 | 0.61s | 0.2% |
+| Refine | 100 | 4.68s | 1.5% |
+| Set solid particle position | 500 | 3.34s | 1.1% |
+| Set tracer particle motion | 501 | 0.729s | 0.24% |
+| Setup dofs | 101 | 2.2s | 0.73% |
+| Solve | 501 | 164s | 54% |
+---------------------------------+-----------+------------+------------+
@endcode
-You may notice that assembling the coupling system is roughly as expensive as
-assemblying the Stokes part, and roughly as expensive as tracking the motion
-of the particles.
+You may notice that assembling the coupling system is more expensive than
+assembling the Stokes part. This depends highly on the number of gauss points
+(solid particles) that are used to apply the Nitsche restriction.
+In the present case, a relatively low number of tracer particles are used.
+Consequently, tracking their motion is relatively cheap.
+
+The following images present the initial and the final configuration of the
+simulation domain:
+
+
+
+
+

+
+
+
+
+
+
+

+
+
+
+We see that, generally, the tracer particles have somewhat returned to their
+original position, although they have been distorted by the flow field.
+The following image compares the initial and the final position of the particles
+after 1s of flow.
+
+
+
+
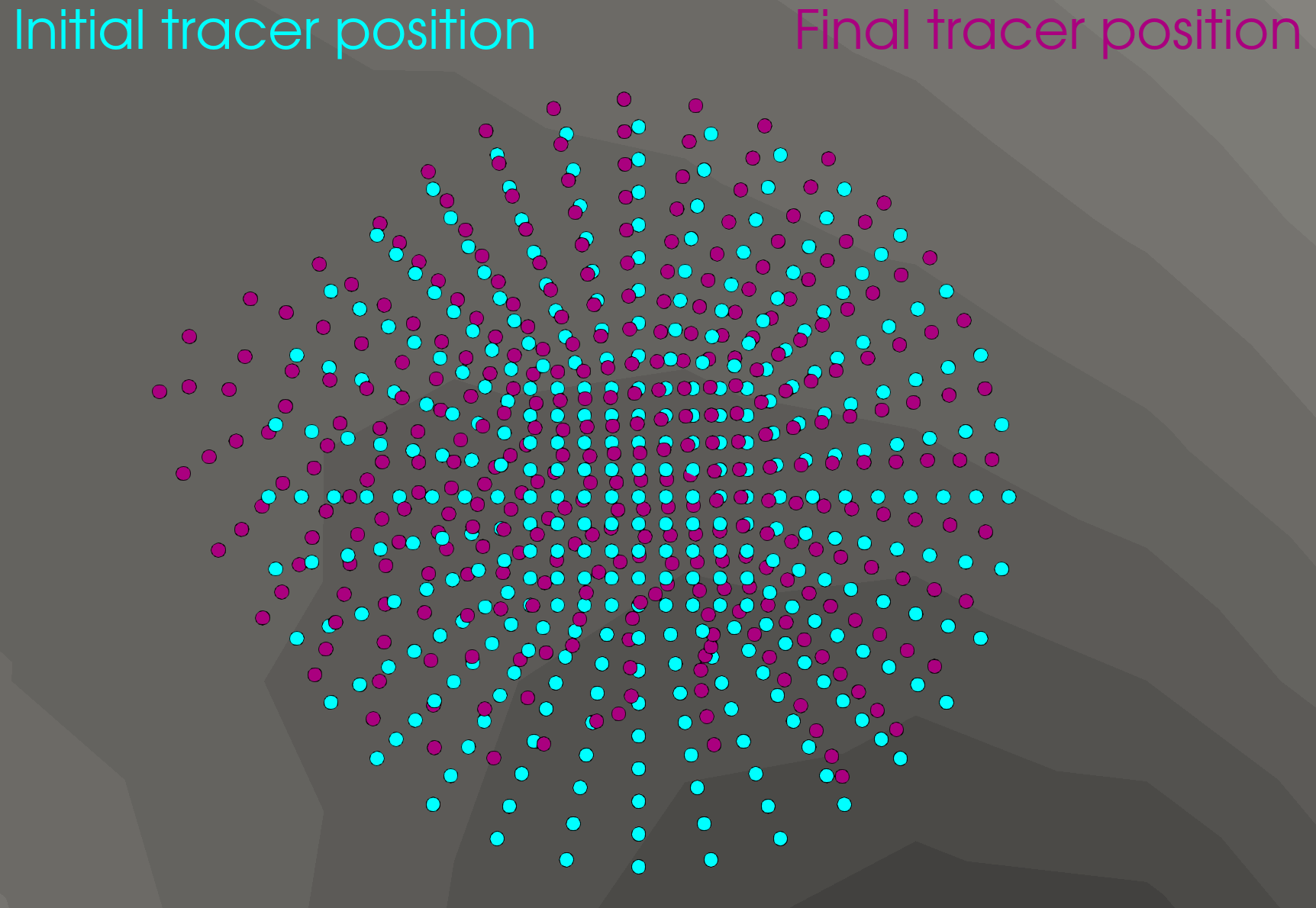
+
+
+
+In this case, we see that the tracer particles that were outside of the swept volume of the
+impeller have returned very close to their initial position, whereas those in the swept
+volume were slightly more deformed. This deformation is non-physical. It is caused by
+the numerical error induced by the explicit Euler scheme used to advect the particles,
+by the loss of accuracy due to the fictious domain and, finally, by the discretization
+error on the Stokes equations. The first two errors are the leading cause of this deformation
+and they could be alleviated by the use of a finer mesh and a lower time step.
+
+ Three dimensional test case
To play around a little bit, we complicate the fictitious domain (taken from
https://grabcad.com/library/lungstors-blower-1), and run a co-dimension one
diff --git a/examples/step-70/parameters.prm b/examples/step-70/parameters.prm
index 806468b87e..3234de62c4 100644
--- a/examples/step-70/parameters.prm
+++ b/examples/step-70/parameters.prm
@@ -1,26 +1,38 @@
subsection Stokes Immersed Problem
set Final time = 1
- set Homogeneous Dirichlet boundary ids = 0, 1, 2, 3
- set Initial fluid refinement = 4
- set Initial solid refinement = 4
+ set Homogeneous Dirichlet boundary ids = 0
+ set Initial fluid refinement = 5
+ set Initial solid refinement = 5
set Particle insertion refinement = 4
- set Nitsche penalty term = 200
+ set Nitsche penalty term = 100
set Number of time steps = 501
set Velocity degree = 2
set Viscosity = 1
subsection Angular velocity
set Function constants =
- set Function expression = t < .500001 ? 5 : -5
+ set Function expression = t < .500001 ? 6.283185 : -6.283185 # default: 0
set Variable names = x,y,t
end
subsection Grid generation
- set Grid one generator = hyper_cube
- set Grid one generator arguments = -1: 1: false
- set Grid two generator = hyper_rectangle
- set Grid two generator arguments = -.5, -.1: .5, .1: false
+ set Fluid grid generator = hyper_cube
+ set Fluid grid generator arguments = -1: 1: false
set Particle grid generator = hyper_ball
set Particle grid generator arguments = 0.3, 0.3: 0.1: false
+ set Solid grid generator = hyper_rectangle
+ set Solid grid generator arguments = -.5, -.1: .5, .1: false
end
+
+ subsection Refinement and remeshing
+ set Maximum number of cells = 20000
+ set Refinement coarsening fraction = 0.3
+ set Refinement fraction = 0.3
+ set Refinement maximal level = 8
+ set Refinement minimal level = 5
+ set Refinement step frequency = 5
+ set Refinement strategy = fixed_fraction
+ end
+
+
subsection Right hand side
set Function constants =
set Function expression = 0; 0; 0
diff --git a/examples/step-70/step-70.cc b/examples/step-70/step-70.cc
index ff328880b3..6f4f76e5f1 100644
--- a/examples/step-70/step-70.cc
+++ b/examples/step-70/step-70.cc
@@ -60,10 +60,10 @@ namespace LA
#include
#include
+#include
#include
#include
#include
-#include
#include
#include
@@ -205,7 +205,7 @@ namespace Step70
// elasticity model in this tutorial, and transform it into a fully fledged
// FSI solver.
unsigned int initial_fluid_refinement = 5;
- unsigned int initial_solid_refinement = 3;
+ unsigned int initial_solid_refinement = 5;
unsigned int particle_insertion_refinement = 3;
// To provide a rough description of the fluid domain, we use the method
@@ -281,7 +281,9 @@ namespace Step70
// Similarly, we allow for different local refinement strategies. In
// particular, we limit the maximum number of refinement levels, in order
// to control the minimum size of the fluid grid, and guarantee that it is
- // compatible with the solid grid. Additionnaly, we perform local refinement
+ // compatible with the solid grid. The minimum number of refinement levels
+ // is also controlled to ensured sufficient accuracy in the
+ // bulk of the flow. Additionnaly, we perform local refinement
// based on standard error estimators on the fluid velocity field.
//
// We permit the user to choose between the
@@ -292,11 +294,12 @@ namespace Step70
//
// Refinement may be done every few time steps, instead of continuously, and
// we control this value by the `refinement_frequency` parameter:
- int max_level_refinement = 7;
+ int max_level_refinement = 8;
+ int min_level_refinement = 5;
std::string refinement_strategy = "fixed_fraction";
double coarsening_fraction = 0.3;
double refinement_fraction = 0.3;
- unsigned int max_cells = 1000;
+ unsigned int max_cells = 20000;
int refinement_frequency = 5;
// These two functions are used to control the source term of Stokes flow
@@ -1439,8 +1442,14 @@ namespace Step70
}
for (const auto &cell : fluid_tria.active_cell_iterators())
- if (cell->refine_flag_set() && cell->level() == par.max_level_refinement)
- cell->clear_refine_flag();
+ {
+ if (cell->refine_flag_set() &&
+ cell->level() == par.max_level_refinement)
+ cell->clear_refine_flag();
+ if (cell->coarsen_flag_set() &&
+ cell->level() == par.min_level_refinement)
+ cell->clear_coarsen_flag();
+ }
parallel::distributed::SolutionTransfer
transfer(fluid_dh);
@@ -1743,6 +1752,7 @@ namespace Step70
this->prm.enter_subsection("Refinement and remeshing");
this->prm.add_parameter("Refinement step frequency", refinement_frequency);
this->prm.add_parameter("Refinement maximal level", max_level_refinement);
+ this->prm.add_parameter("Refinement minimal level", min_level_refinement);
this->prm.add_parameter("Refinement strategy",
refinement_strategy,
"",
@@ -1761,8 +1771,10 @@ namespace Step70
spacedim + 1);
});
// and define a meaningful default angular velocity instaed of zero
- angular_velocity.declare_parameters_call_back.connect(
- [&]() { this->prm.set("Function expression", "t < .500001 ? 5 : -5"); });
+ angular_velocity.declare_parameters_call_back.connect([&]() {
+ this->prm.set("Function expression",
+ "t < .500001 ? 6.283185 : -6.283185");
+ });
}
} // namespace Step70